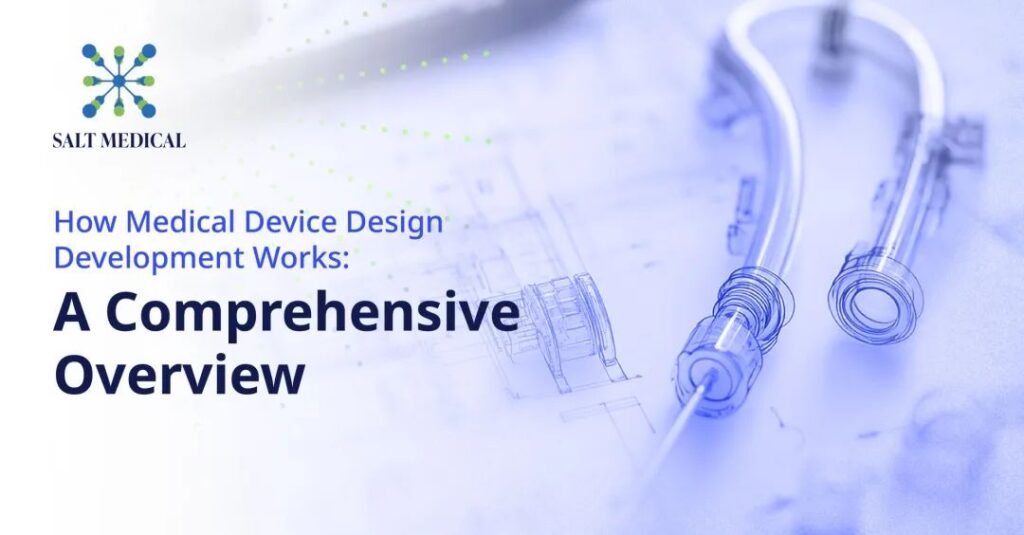
In the field of medical devices, every product must go through a complex and sophisticated design and manufacturing process from concept to mass production, and Design for Manufacturing (DFM) is the core link in this process. It not only ensures that the product can be manufactured within the target manufacturing cost, but also meets regulations, usability and patient experience while ensuring quality, safety and performance.
The main goals of DFM are:
The main goal of DFM is to make product manufacturing simpler and faster with as few steps as possible in the manufacturing process. For the number of parts, design engineers will eliminate or combine components to ensure that as few parts as possible are used, which saves production and assembly time and steps and reduces the risk of errors. In addition to part reduction, part standardization is also one of the main goals of DFM
Introducing DFM early: twice the result with half the effort
It is crucial to incorporate DFM principles into the initial planning of a project, which can effectively avoid time delays and cost increases caused by later design modifications. For example, if the design is forced to be adjusted later to meet manufacturing requirements, it will not only delay the progress, but may also cause the project to overspend. Therefore, integrating DFM as early as possible can effectively avoid potential risks, optimize processes, and speed up the product from concept to market.
Eight questions about DFM: Make your design stand up to scrutiny
When designing a new medical device product, a DFM approach requires us to question every aspect of the product and design:
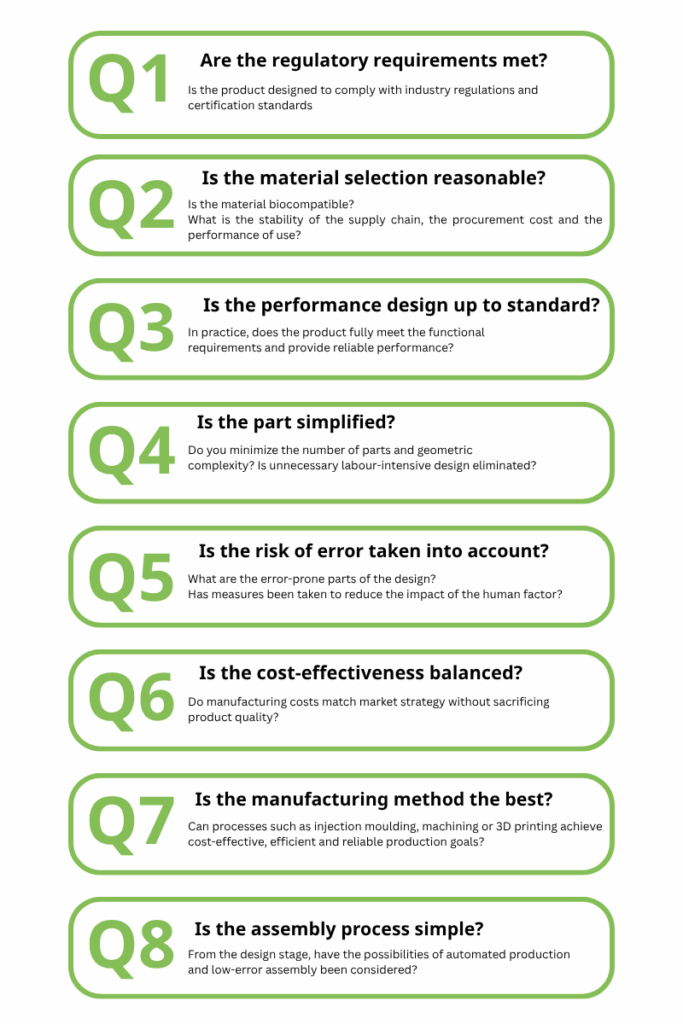
Factors to consider during the DFM process
Regulations
The design must comply with all relevant regulations and standards, such as FDA or CE certification requirements.
Materials
In minimally invasive medical device products, materials must be safe and biocompatible.Selecting the right materials will also have an impact on product performance, as different materials and material combinations will have different performance characteristics. The availability of materials in the supply chain, as well as procurement costs and materials, must also be considered.
Performance
The product should function as intended and in realistic situations according to its defined functional requirements.
Simplification of parts
Minimise the number of parts. Minimise part complexity and any other features that would make the medical device more difficult to manufacture and/or assemble.
Avoid complex geometries or designs with high labor dependency and use standardised components.
Reduce and eliminate the risk of errors
Engineers need to consider the manufacturing process from beginning to end to identify and evaluate potential errors. Emphasis will be placed on those parts of the manufacturing and assembly process that have a human element. When the risk of human error is identified, engineers need to consider how to reduce or eliminate the risk.
Cost-effectiveness
Don’t just focus on the cost of each individual product or component, but also consider production volume, yield, reliability of the manufacturing process, and overall product quality. The goal is to ensure that manufacturing costs are aligned with the product’s commercial strategy without compromising safety, quality, or compliance.
Manufacturing process
Choose the appropriate manufacturing process according to the product characteristics, i.e. machining, injection molding, 3D printing, etc. At the same time, ensure that the tolerance range is moderate.
Assembly process
Design for manufacturing and assembly (DFMA) considers minimizing steps and components, making design adjustments to facilitate automation, reduce potential errors, and make the process as simple as possible.
Process compatibility
Take into account current manufacturing capabilities. The aim is to minimize the need for new equipment or skills.
Design compliance
The design of new medical device products must comply with good manufacturing practices (GMP). For example, the design needs to consider the practicalities of manufacturing components and then processing them for assembly.
Post-DFM process still needs to be fully optimized
DFM is not only important in the design phase, but its subsequent implementation also needs to focus on the following aspects:
Design transfer and validation: First article inspection (FAI) ensures consistency and reliability in mass production, where production processes must be validated to ensure they produce products or components as specified.
Operator Training: Employee training as well as ongoing performance monitoring and continuous improvement are also critical for operators involved in the production and assembly processes.
Supply Chain Management: Supply chain is an important part of the DFM process and decision making, which includes not only the availability of materials when everything is running smoothly, but also the availability of materials when challenges arise, potential bottlenecks in the supply chain.
Reference: Whitepaper-Three Essential Phases of Medical Device Manufacturing Success
At Salt Medical, we believe that smart design is the foundation of successful manufacturing—and Design for Manufacturability (DFM) is where that success begins. Whether you’re developing a complex minimally invasive device or looking to refine an existing product, our team brings the technical expertise, cleanroom capability, and global supply chain strength to help you accelerate development, reduce risk, and meet market demands. If you’re looking for a proactive, precision-driven CDMO partner who can support you from early concept to scalable production, we’d love to hear from you. Let’s build the future of medtech—together.
Interested to Learn More About Salt Medical? Contact Us